We did some research to answer the question, how successful organizations do maintenance & reliability management.
Here is what we came up with:
Planning & Implementation
Successful organizations take the implementation of new processes and programs very seriously. They spend more time planning, developing, documenting, and agreeing on what to do than actually doing it. Most of the time is spent on the implementation of long-term reliability and maintenance plans.
Reliability-centered maintenance (RCM), for instance, is a sound and proven method for allocating maintenance and reliability resources to align with the organization’s mission. RCM has gained extreme popularity within the last years and has an essential part in maintenance.
Precision Standards & Precision Maintenance
Precision maintenance is best thought of as a cultural framework for maintaining reliable, consistent, and efficient equipment results.
A successful precision maintenance program’s foundation is documented standard operating procedures (SOPs) that leave no room for error.
Precision maintenance SOPs should be detailed, accessible, and up to date. Articulated SOPs, and proper team training, guarantee consistent task outcomes regardless of who is completing a work order, which leads us to another critical key success factor: Training.
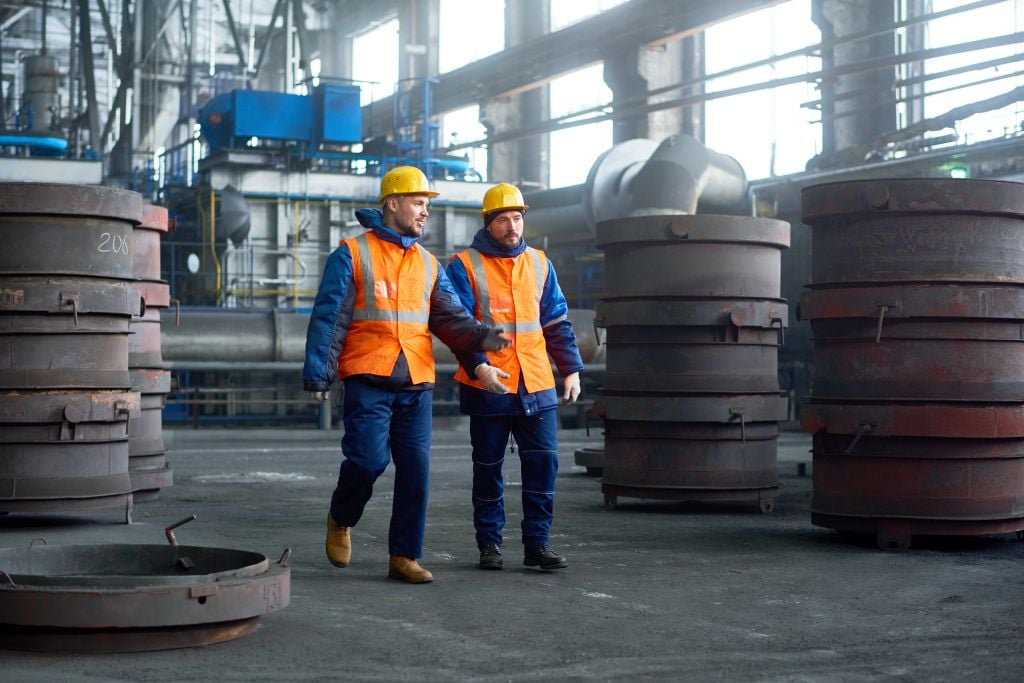
Training
Onboarding and training new employees are crucial if you want to optimize your maintenance.
Maintenance approaches are often expert-centric. Often, one or just a few experts have gained critical expertise for specific machines, plants, or processes over the years they have been with the company. This kind of in-depth knowledge acquires many years of professional experience. Newcomers and less experienced maintenance personnel lack this specialized expert knowledge, which is particularly useful in critical situations. If companies and teams do not manage to transfer this knowledge in time, before the experts leave the company, all the specialized experience is irretrievably lost.
Training new employees ensures that they stick to the same procedures and are able to detect and eliminate defects immediately.
Continuous improvement & measuring results
The key to being successful with your activities is to evaluate and improve your performance continuously. The most effective way to measure results is with key performance indicators (KPIs), such as:
- Number of improvement work orders completed monthly
- Reduced energy consumption
- Reduced overall vibration levels
- Meantime between failures (MTBF)
- Reduced downtimes incl. financial benefits
- Increased incremental production
- Reduced manufacturing costs
Work smarter
Digital tools support employees’ maintenance and reliability in their daily tasks, helping them be more efficient. We have developed Partium, our mobile spare part search, to drive digitization in maintenance environments. Our software enables technicians to identify spare parts within seconds through a camera search on their phone. They can snap a picture; our AI will identify the part and give them an article number/SKU and link them into the EAM/ERP or warehouse system, where they can access maintenance-related notes and documentation.
It’s a neat solution that helps technicians cut down on failed part identifications, search times and warehouse trips, and all the overhead related to part searches.
Do you want to know more about Partium? Please shoot us a message; we are looking forward to discussing your personal use case together!